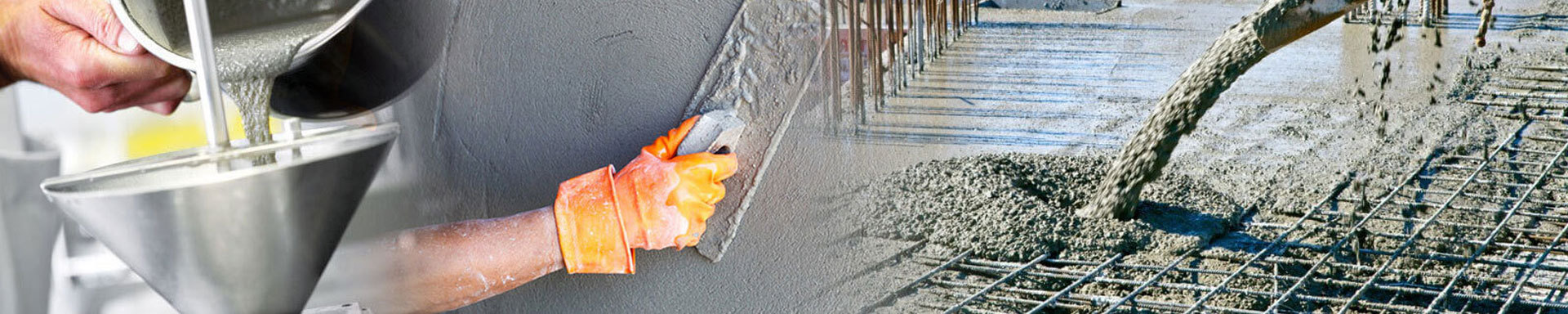
- Home
- >
News
In recent years, with the continuous development of external insulation technology, hydroxypropyl methyl cellulose production technology progress, as well as hydroxypropyl methyl cellulose HPMC itself has excellent characteristics, hydroxypropyl methyl cellulose HPMC in the construction industry has been widely used. In order to investigate the interaction mechanism between HPMC and cement-based materials, this paper focuses on the improvement effect of HPMC on the cohesion of cement-based materials.
High-quality HPMC can be evenly and effectively dispersed in cement mortar and gypsum based products, and wrap all solid particles, and form a layer of wetting film. The moisture in the base is gradually released over a long period of time, and hydrates with inorganic cementitious materials, thus ensuring the bonding strength and compressive strength of the materials. Therefore, in high temperature summer construction, in order to achieve the water retention effect, it is necessary to add enough high-quality HPMC products according to the formula, otherwise, quality problems such as insufficient hydration, strength reduction, cracking, hollowing and falling off caused by drying too fast will occur, and the construction difficulty of workers will also be increased. As the temperature decreases, the amount of HPMC can be gradually reduced, and the same water retention effect can be achieved.
Enhance the adhesion with the masonry surface, and can enhance the water retention, so that the strength of mortar can be improved. Improve the lubricity and plasticity to improve the construction performance, save time and improve the cost efficiency.
Cold water instant HPMC can be used for putty powder, mortar, liquid glue, liquid paint and daily chemical products. Hot melt HPMC is usually used in dry powder products and directly mixed with dry powder for uniform application, such as putty powder and mortar. Hydroxypropyl methyl cellulose can be widely used to improve the performance of cement, gypsum and other hydrate building materials. In cement-based mortar, it can improve water retention, extend correction time and opening time, and reduce flow suspension.
The water retention effect of HPMC depends on the water absorption of the base course, the composition of the mortar, the thickness of the mortar layer, the water demand of the mortar, and the setting time of the setting material. The water retention of HPMC itself comes from the solubility and dehydration of HPMC itself.
In the dry mixed ready mixed mortar, the addition of hpmc is very low, but it can improve the performance of wet mortar. The reasonable selection of different varieties, different viscosities, different particle sizes, different viscosities and different amounts of cellulose ethers has an impact on the improvement of the performance of dry powder mortar. At present, many masonry and plastering mortars have poor water retention performance, and water slurry separation will occur after a few minutes of standing. Water retention is an important performance of methyl cellulose ether, and it is also the performance concerned by many domestic dry powder mortar manufacturers, especially those in the regions with high temperature in the south. The factors affecting the water retention effect of dry powder mortar include the amount of hpmc, the viscosity of hpmc, the fineness of particles and the temperature of the environment. Hydroxypropyl methylcellulose (hpmc) is a kind of synthetic polymer, which is made from natural cellulose by chemical modification.
In dry mixed ready mixed mortar, the addition of hpmc is very low, but it can improve the performance of wet mortar. The reasonable selection of different varieties, different viscosities, different particle sizes, different viscosities and different amounts of cellulose ethers has an impact on the improvement of the performance of dry powder mortar. At present, many masonry and plastering mortars have poor water retention performance, and water slurry separation will occur after a few minutes of standing. Water retention is an important performance of methyl cellulose ether, and it is also the performance concerned by many domestic dry powder mortar manufacturers, especially those in the regions with high temperature in the south. The factors affecting the water retention effect of dry powder mortar include the amount of hpmc added, the viscosity of hpmc, the fineness of particles and the temperature of the use environment. Hpmc is a kind of synthetic polymer, which is made from natural cellulose by chemical modification.
HPMC products for construction are widely used to improve the performance of hydraulic building materials, such as cement and gypsum. In cement-based mortar, it can improve water retention, extend correction time and opening time, and reduce sagging phenomenon.