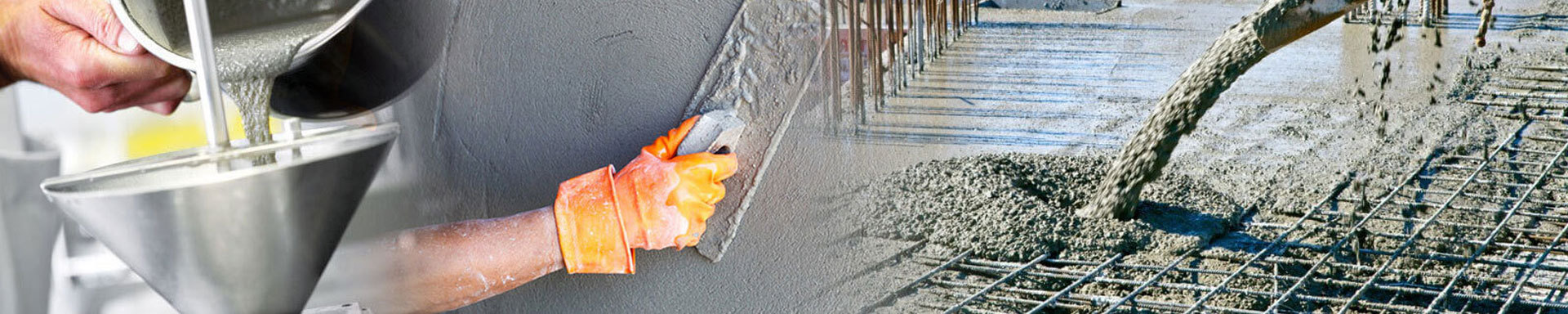
Factors affecting the viscosity of PVC paste resin
2024-05-29 09:57PVC paste resin is widely used in artificial leather, wallpaper, floor leather, canvas coating, battery separator, industrial conveyor belt, boots, gloves, toys and other fields. PVC paste resin is generally processed in the form of plasticized paste. The molding methods include dip molding, coating, slush molding and spraying. The viscosity of the plasticized paste under specific conditions is usually used to evaluate the processing performance of the paste.
(1) As the pH value of the polymerization reaction system increases, the thermal decomposition temperature of the resin increases, the stability improves, the polymerization time is prolonged, the median particle size decreases, and the paste viscosity increases. When the pH value is greater than 7, the thermal decomposition temperature of the resin continues to increase, the polymerization time is prolonged, but the median particle size and paste viscosity of the resin change very little. Taking all factors into consideration, the pH value of the polymerization reaction system is more suitable at around .
(2) The viscosity of Polyvinyl Chloride Paste Resin increases with the increase of the amount of emulsifier, but after a certain amount, the median particle size and paste viscosity of the resin do not change significantly. Continuously increasing the amount of emulsifier cannot achieve the purpose of adjusting the paste viscosity. The amount of emulsifier has little effect on the paste viscosity at low shear rate, but has a sensitive effect on the paste viscosity at high shear rate.
(3) When the formula of PVC paste resin is determined, different homogenizing equipment can be used to produce resins with different particle size distributions and paste viscosities.
(4) Properly increasing the drying inlet temperature of PVC paste resin and reducing the drying outlet temperature are beneficial to reducing the viscosity of resin paste. The selection of drying inlet and outlet temperatures should comprehensively consider factors such as latex solid content and drying system wind speed.